Smart Well Controller and POC
SWC – (SRP, ESP, PCP)
ADVANTAGES- Utilizes the same Added Value Applications & Solutions
- (AVAS) as the CILA2S
- Ability to work with any pump design and manufacturer
- Ability to work with any VSD brand
- Ability to work with any surface or downhole sensor
- Ability to operate with different brands and technologies
- of induction and permanent magnet motors
- Cost-effective artificial lift controller
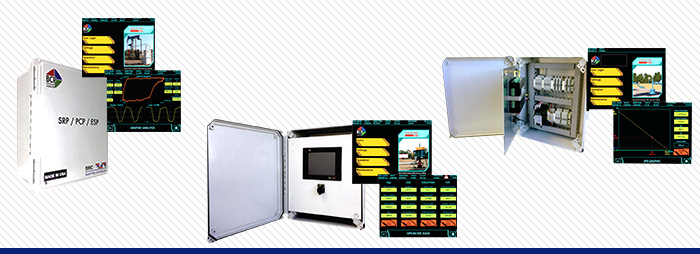
- Independent upstroke and downstroke speed variation for buoyancy Of the rod String
- Sensorless fluid level estimation With pressure monitoring and/or Echometer results
- 3D Dynagraph for analysis of state of rods, fatigue points, and effective pumping
- Surface downhole visualization cards and diagnostics with smart pump off control
- Statistical analysis of failures. Anomalies prediction through on site trajectory of the well behaviour
- Well IPR on site and speed adjustment suggestions
- Goodman analysis for rod protection rod stress from surface to downhole
- Production rate estimation using pump efficiency and stroke speed calculation
- Different field instrumentation compliance (Dual independent for load and position)
- Signals verification for correct cards display
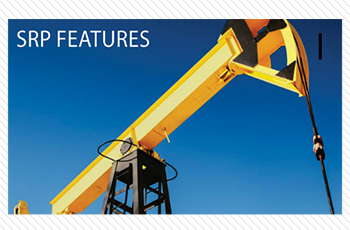
- Intelligent torque control for automatic speed adjustments
- Configurable start up speed ramps (Staggered start up ramps)
- Extended speed reference changes
- Multiple automatic startups (speed ramp and execution time) configuration when shot down
- Nomographic Chart for PCP System diagnostics
- Well IPR on site and speed adjustment suggestions
- Intelligent well optimization control for automatic speed variation according to well inflow
- Build up test capabilities
- Sensorless technology for fluid level and submergence
- Closed loop control for diluent supply
- Downhole sensor data connection ready for plug and play
- Sensor data connection ready for and play control mode
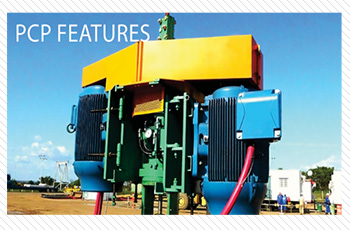
- Pwf control rnode
- Alternative start up modes for stuck pump
- Configurable start up ramps (staggered start up ramps)
- Well IPR on site and speed adjustment suggestions
- Intelligent well optimization control for automatic speed variation to well inflow
- Sensorless technology and downhole pump/well parameter calculations
- Online view and performance curves of the pump
- Downhole sensor data connection ready for plug and play
- Extended speed reference charges
- Automatic rotation direction Analysis
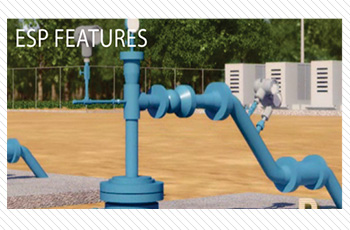
POC Functionality
Surface and Downhole Dynagraph Generation– Generation of surface and downhole dynagraphs. Used in statistical analysis of pump trajectory and anomalies detection.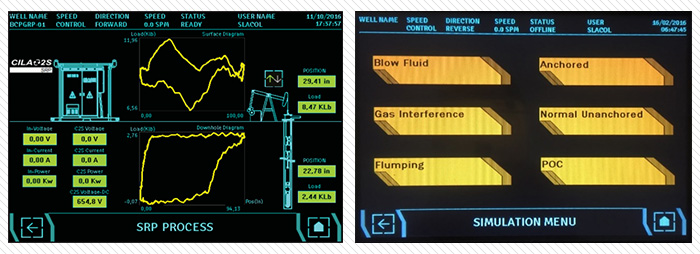
Pump Fillage %
Calculates pump fillage based on dynagraph interpretation and change over time. Can set pump off limit with point on dynagram or with minimum pump fillage % value.
Sensorless Fluid Level Estimation
Estimates dynamic fluid level using casing and tubing pressures (from manual input or connected sensor input), fluid properties, load, position, and pump information. Can also be calibrated with echometer results for even more accurate and long term reliable estimation.
Production Rate Estimation
Estimate production using pump fillage/efficiency on each stroke and stroke speed.
Pump Trajectory and Anomalies Detection
Neural Network based pump status analysis and visualization onto a Cartesian grid. Monitors status and conditions regarding the type of failure or potential failure.
3D Dynagraph
Gives information about the state of the rods, fatigue points, and its effective pumping. Goodman analysis visualization on-site for tapered designs.
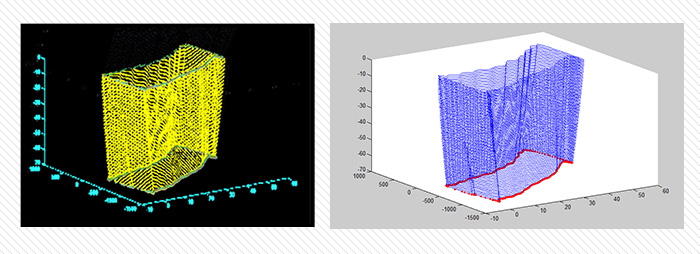
IWOC – Intelligent Well Optimization Control
The IWOC follows a series of algorithms, rules and mathematical models of each Artificial Lift method, that allows the optimizer to make decisions on how to operate and control its oil production wells through the Artificial Lift system installed and identify actions to make real time optimization. Considering reservoir parameters, real-time behavior of the motor/pump and surface conditions, the system generates:
Generate Inflow Performance Relationship chart (IPR) and / or Nodal Analysis, with the trajectory of behavior, showing the last three conditions of nodal.
- Perform the production optimization through system monitoring and remote control (SCADA) through the integration and communication capabilities depending on the level of automation available.
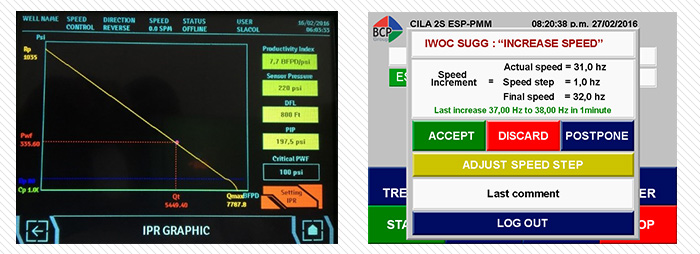