Cila 2S
CILA 2S
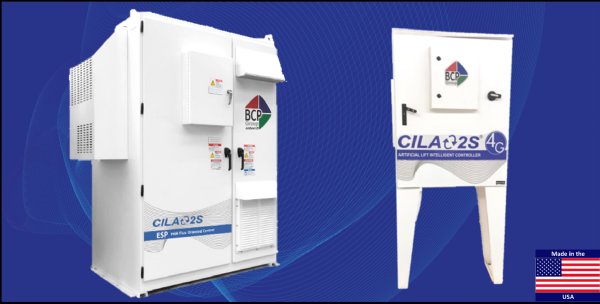
The CILA2S is compatible with all motor types (IM and PMM), motor brands, pumps, and sensors. We have proven compatibility with all induction motors and over 10 different PMM motors to date. Our PMM Flux Oriented Control is the only patented firmware that has proven to maintain a power factor of 1 completely independent of load.
Power Sags Ride-Thru The CILA 2S system maintains operational continuity on a power loss failure (to 0 volt) up to 1500+ milliseconds at full load.
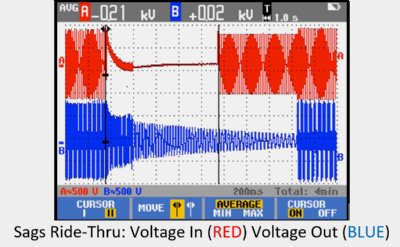
- Speed increment recommendations based on the downhole pressure behavior to increase production and protect the assets.
- Generates Inflow Performance Relationship chart (IPR) and / or Nodal Analysis, with the trajectory of behavior, showing the last three conditions of nodal.
- Executes production optimization through automated system monitoring or remote control (SCADA) through the integration and communication capabilities depending on the level of automation available.
- High High (HH) causes Stop.
- High (H) causes Alarm.
- Low (L) causes Alarm.
- Low Low (LL) causes Stop.
Low Harmonics 6 Pulse drive (others available) most commonly utilized. With harmonics filters, THD meets IEEE requirements down to 30% of the load
Low Voltage and Medium Voltage The CILA2S is capable of Low Voltage and Medium Voltage applications maintaining unmatched performance and the same availability of functions.
Sucker Rod Pump Functions
The control algorithms within the CILA2S SRP incorporate all aspects of artificial lift engineering including online surface and subsurface operative data, power quality energy monitoring, Scada system connectivity compliance, optimization control algorithms, online diagnostics with pump status graphic visualizations, online trending, electrical/process configurable protections, and selectable control modes for SRP performance.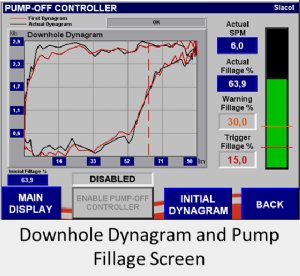
ESP Functions
CILA2S ESP BrochureThe control algorithms within the CILA2S ESP incorporate all aspects of artificial lift engineering including online surface and subsurface operative data, power quality energy monitoring, Scada system connectivity compliance, optimization control algorithms, online diagnostics with pump status graphic visualizations, online trending, electrical/process configurable protections, and selectable control modes for ESP performance.
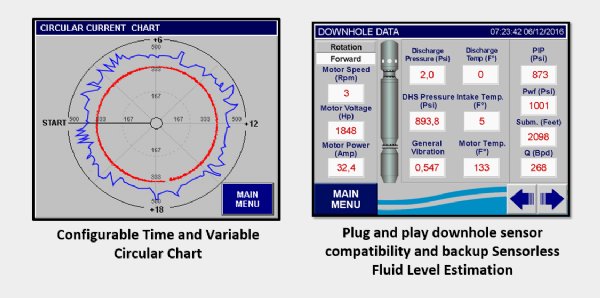
Startup and Restart Modes
Advanced Startup and Restart modes to ensure careful handling of pump for all ramp-up situations:
- Reverse Direction Start
- Rocking Start
- Staggered Ramp Start
Staggered Step Ramp Startup
Safe and controlled start to allow stabilization of the well before reaching desired speed.
Automatic Rotation Direction Analysis
The CILA2S controller Rotation Direction Analysis algorithm is a program to record and display variable measurements at configurable times to automatically determine the correct direction of the Electric Submersible Pump.
Intelligent RunLife (iRL)
With the iRL Runlife, the operator can visualize the behavior of the operation equipment to identify and predict possible failures and prevent them through operation regime pre-configured for process variables.
It can perform traceability of startups attempts and maintenance dates, thanks to operational times and downtimes (monthly/yearly registered) during the lifetime of the well
Nomographic Chart
BCP Group unique and exclusive tool for visual diagnostics of the actual status of the well/artificial lift system, using colored regions.
Circular Current Chart
View the current and other key parameters in a configurable time circle chart
Gas Lock Avoidance
Gas lock prevention based on load and additional key indicator variables
Operation Variable Trending
It is possible to visualize the online trends of operational variables both from the VSD and processes on the screen of the CILA2S
PCP Functions
The control algorithms within the CILA2S PCP incorporate all aspects of artificial lift engineering including online surface and subsurface operative data, power quality energy monitoring, Scada system connectivity compliance, optimization control algorithms, online diagnostics with pump status graphic visualizations, online trending, electrical/process configurable protections, and selectable control modes for PCP performance.Nomographic Chart
BCP Group unique and exclusive tool for visual diagnostics of the actual status of the well/artificial lift system, using colored regions.
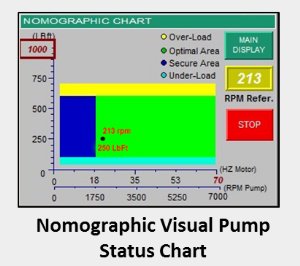
Algorithm developed from wells in the most challenging heavy oil reservoirs in the world to protect and optimize the pump against backspin phenomena.
PCP System Intelligent Torque Control (ITC) Protection
Constant monitoring of the Rod system torque in PCP, specifically in transmission rods. This controls logic executes speed to protect the PCP when in presence of high torque levels, thus protecting the integrity of the artificial lift system and avoiding possible rupture.
Stepped Ramp Start and Restarts
This control logic is dedicated to automatic startup by time steps. It allows for stabilization of the Artificial Lift system and the well before reaching the required operating speed.
Circular Current Chart
View the current and other key parameters in a configurable time circle chart
Intelligent RunLife (iRL)
With the iRL Runlife, the operator can visualize the behavior of the operation equipment to identify and predict possible failures and prevent them through operation regime pre-configured for process variables.
Operation Variable Trending
It is possible to visualize the online trends of operational variables both from the VSD and processes on the screen of the CILA2S
Permanent Magnet Motor Capabilities
We have the only proven controller solution with closed-loop-Flux Oriented Control (F.O.C.) for permanent magnet motor artificial lift systems (Downhole Driven Permanent Magnet Motor PCP's and PMM-ESP's)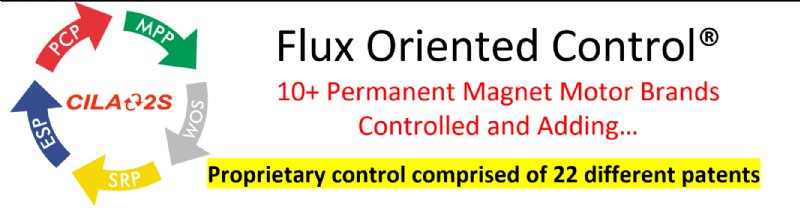
-
+ Ideal sinusoidal motor current eliminates current interruption and therefore lots of harmonics. This ensures optimal motor efficiency ALWAYS.
+ Utilize motor reluctance torque properly (increases the motor torque capability).
+ No limit for cable length.
+ Enhance motor starting process.
+ Increase accuracy of speed estimation
+ Better control of transformer inrush current and saturation
+ Better dynamic performance due to vector control
CILA2S PMM Versatility
-
The CiLA2S is currently controlling 3 different brands of PMM's in the field with unmatched control with more already proven in the lab. This includes both surface and internal mounted PM motors. The CILA2S is able to control different brand motors for ESP-PMM's, ESPCP-PMM's, and Surface PCP-PMM's.
CILA2S PMM Field Results
-
With the patented Flux Oriented Control, the power factor is always 1 regardless of the load. For wells with oversized motors, noticeable gas or light oil production, or operating at lower speeds as shown below, the efficiency still remains extremely close to 1.
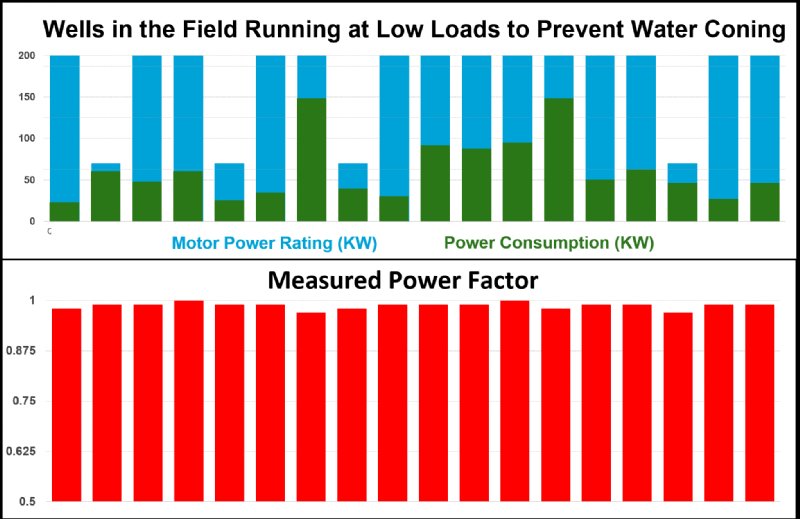
-
At our Houston manufacturing and testing headquarters, we are able to test any ESP or surface/downhole PCP motor (IM/PMM), pump, drive, or sensor for compatibility, software development, and efficiency evaluation. We are able to simulate various loads and electrical sags to validate performance. Please contact us if you would like a tour of the facility or to test a solution and see the advantage of the PMM Flux Oriented Control.
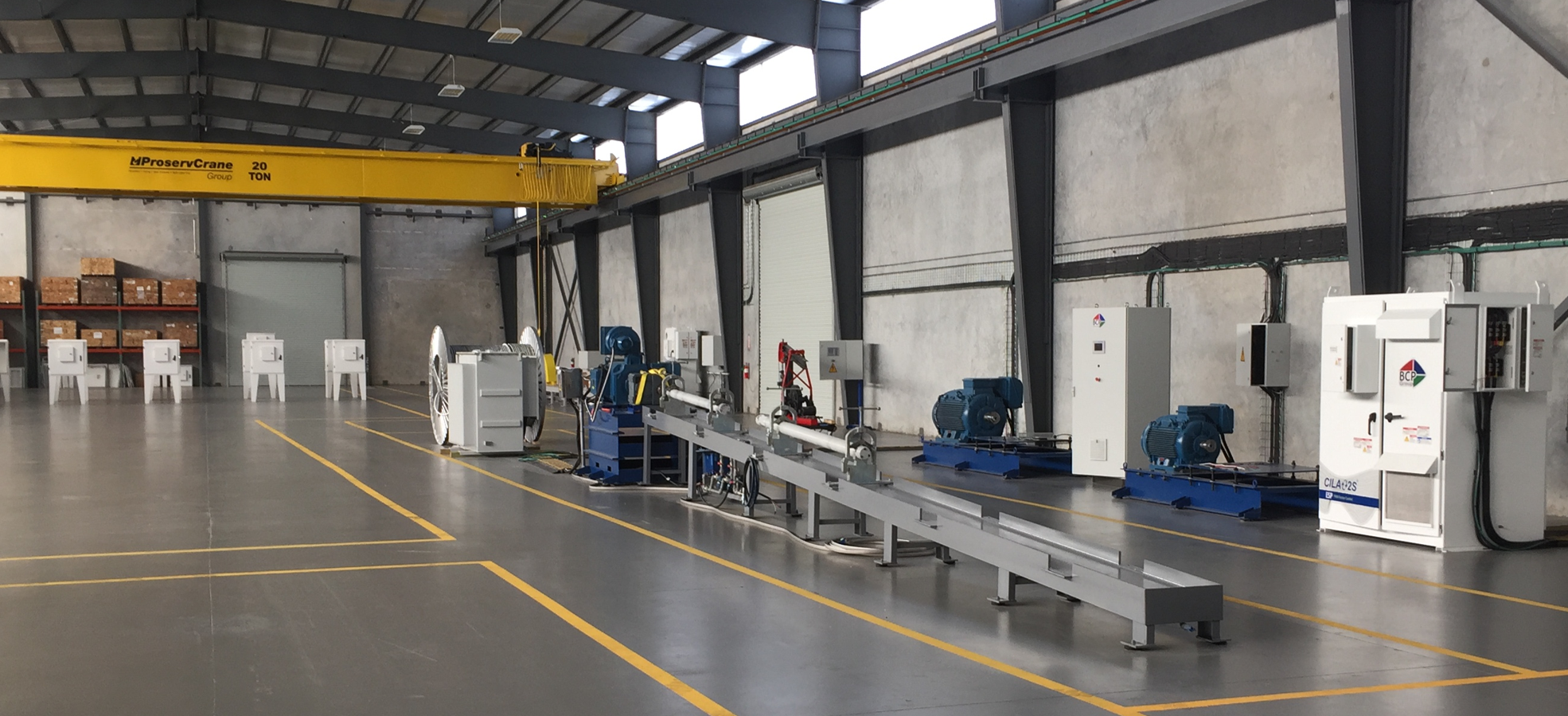